CNC Machining, short for Computer Numerical Control, has revolutionized manufacturing over the decades. What began as a manual process has evolved into a high-tech, automated approach to fabricating complex parts with exceptional precision. Traditional CNC systems required extensive programming and human intervention, limiting their speed and flexibility. However, with advancements in technology, modern CNC machines have become more sophisticated, reliable, and efficient, opening up new possibilities for industries worldwide.
Page Contents
Advancements in CNC Technology: Automation and AI Integration
Automation and AI integration are at the forefront of machining’s future, driving the evolution of the modern shop. Smart manufacturing relies on machines equipped with AI algorithms that can optimize cutting paths, tool selection, and process parameters in real-time. These intelligent systems enhance productivity, reduce material waste, and minimize downtime, ensuring a highly efficient ”CNC Machine Shop”.
Additionally, automated tool changers and robotic arms streamline the production process, further improving overall efficiency and reducing human error.
Enhanced Precision Through Real-time Monitoring and Feedback Systems
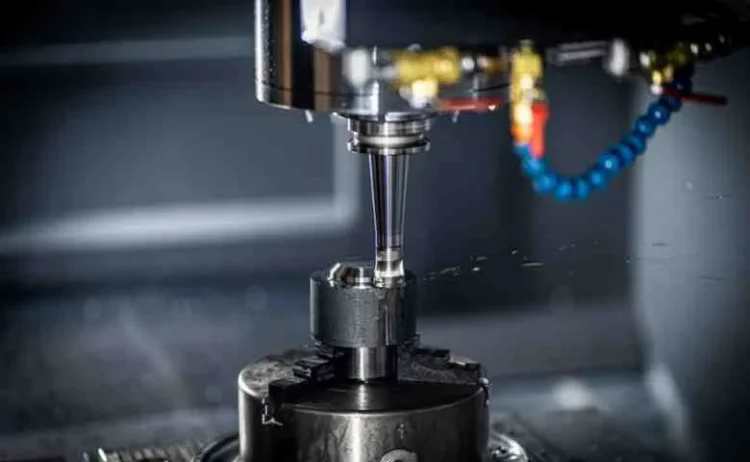
Source: constructionplacements.com
Ensuring utmost precision is crucial in machining, especially for industries like aerospace and medical devices. Real-time monitoring and feedback systems play a pivotal role in achieving this goal. Advanced sensors integrated into machines collect data on temperature, vibration, and cutting forces.
This data is then analyzed in real time, enabling operators to detect anomalies and make immediate adjustments. By continuously fine-tuning the machining process, these feedback systems enhance the accuracy and reliability of the final product, meeting the stringent demands of modern manufacturing.
Green Manufacturing: Sustainable Practices and Eco-friendly Materials
As environmental concerns grow, industries are shifting towards greener manufacturing practices, and machining is no exception. Embracing sustainable practices, such as energy-efficient machining strategies and recycling of materials, helps minimize the environmental impact.
Additionally, manufacturers are exploring eco-friendly materials, like biodegradable plastics and recycled metals, to reduce the carbon footprint further. By adopting green manufacturing principles, the industry can play a significant role in creating a more sustainable future.
Miniaturization Capabilities: Micro-machining and Its Diverse Applications
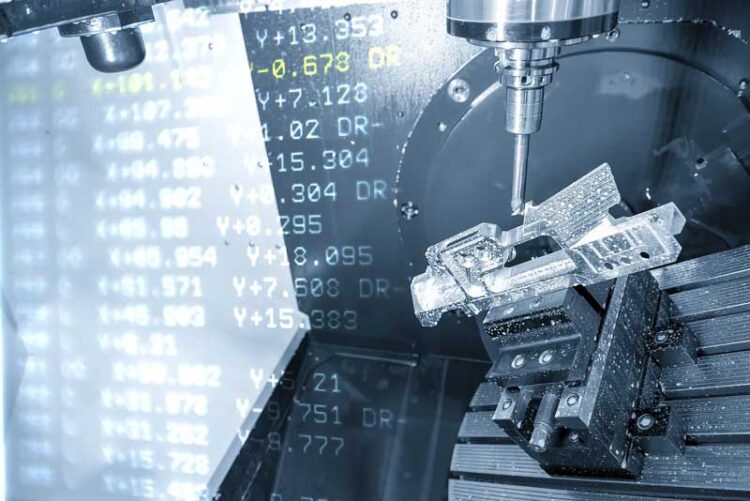
Source: wisconsinmetaltech.com
Miniaturization is a trend that has gained tremendous momentum in recent years, driven by demand for smaller, intricate components in electronics, medical devices, and automotive industries. Micro-machining, a subfield of CNC machining, involves the fabrication of tiny, high-precision parts.
Advancements in technology, including smaller cutting tools and improved motion control systems, have made micro-machining possible. The applications are diverse, ranging from microelectronics and biomedical implants to microfluidics and aerospace components.
Multi-axis Machining: Pushing the Boundaries of Complex Geometries
Traditional CNC machines typically operated with three axes, limiting the complexity of shapes that could be produced. However, multi-axis machining is changing the game by enabling machines to move in multiple directions simultaneously.
This capability allows manufacturers to produce highly complex geometries, such as turbine blades and aerospace components with intricate contours. Multi-axis machining reduces setup times, enhances productivity, and eliminates the need for multiple setups, making it a game-changer for industries requiring intricate and customized parts.
Augmented Reality in CNC Operations: Improving User Experience and Training
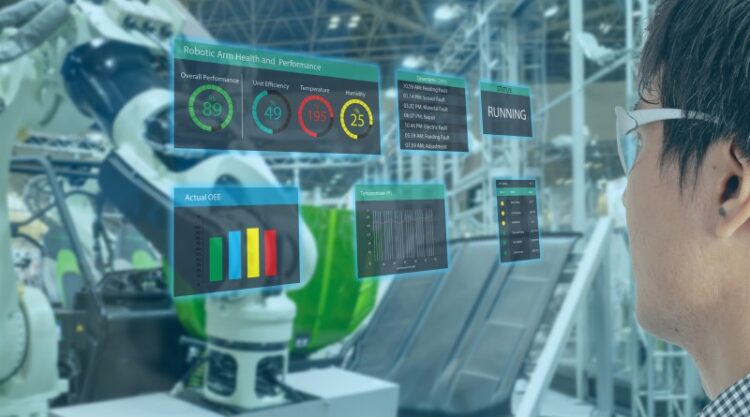
Source: metrology.news
Augmented reality (AR) is transforming CNC operations by providing operators with real-time, contextual information during the machining process. AR overlays digital data, such as tool paths, measurements, and instructions, onto the physical workspace, simplifying complex tasks and reducing errors.
Additionally, AR-powered training programs offer immersive learning experiences for operators, making it easier to acquire new skills and techniques.
Additive Manufacturing Meets CNC: Exploring Hybrid Production Possibilities
The convergence of additive manufacturing (AM) and CNC machining holds enormous potential for the future of manufacturing. Combining these technologies allows for the creation of hybrid machines that can both 3D print intricate structures and perform high-precision finishing.
This approach offers flexibility and efficiency, enabling rapid prototyping and reducing material waste. Moreover, the ability to incorporate different materials, like metals and polymers, in a single process broadens the possibilities for innovative designs and advanced applications across various industries.
Internet of Things (IoT) and Smart Factories Revolutionizing CNC Processes
The Internet of Things (IoT) is transforming traditional CNC factories into smart, interconnected production hubs. IoT-enabled machines and tools communicate with each other, sharing vital data and insights in real-time.
This connectivity streamlines production processes, optimizes resource allocation, and enables predictive maintenance, reducing downtime and maximizing productivity. Smart factories equipped with IoT technology offer unprecedented visibility and control over the entire manufacturing process, facilitating data-driven decision-making and fostering continuous improvement.
Materials Revolution: Utilizing Advanced Alloys and Composites in Machining
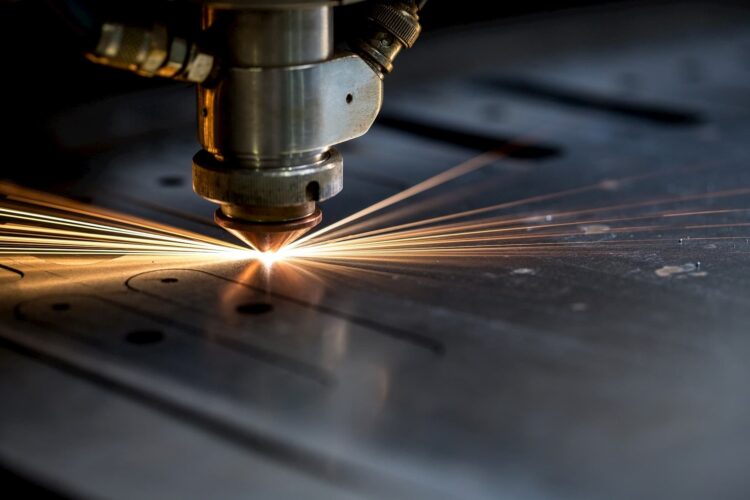
Source: ifm.deakin.edu.au
The future of CNC machining will witness a materials revolution, with the utilization of advanced alloys and composites. These materials possess superior strength-to-weight ratios and unique properties, making them increasingly desirable for high-performance applications.
However, machining these advanced materials can be challenging due to their toughness and abrasive nature. CNC manufacturers are continuously developing cutting tools and machining techniques to overcome these obstacles, unlocking the full potential of advanced materials in various industries, including aerospace, automotive, and renewable energy.
Addressing Challenges: Cybersecurity in the Era of Interconnected CNC Systems
With the rise of interconnected CNC systems and the reliance on digital data, cybersecurity becomes a critical concern. machines are susceptible to cyber threats, such as data breaches, unauthorized access, and malware attacks. Protecting intellectual property and ensuring the integrity of production processes require robust cybersecurity measures.
CNC manufacturers and operators must implement encryption protocols, access controls, and regular system audits to safeguard sensitive information and maintain the trust of customers and partners.
Conclusion
As we delve into the future of CNC machining, we see a landscape brimming with opportunities for innovation and growth. Advancements in automation, AI integration, real-time monitoring, and green manufacturing will drive efficiency and sustainability. Micro-machining, multi-axis capabilities, and augmented reality will push the boundaries of what’s possible in precision manufacturing.
The fusion of additive manufacturing and CNC opens up new horizons for creative designs and rapid prototyping. Meanwhile, the IoT and smart factories promise seamless and data-driven production processes.
Embracing the materials revolution and addressing cybersecurity challenges will be crucial for the CNC industry’s success. The future of CNC machining is undoubtedly exciting, offering a world of possibilities to reshape industries and meet the evolving needs of a diverse global market.
As technology continues to evolve, machining will remain at the forefront of manufacturing, empowering businesses to create innovative, reliable, and sustainable products that shape the world of tomorrow.