Industrial refrigeration maintenance is an important aspect of keeping a business running smoothly. Industrial refrigeration systems are vital for any business that needs to keep its products and services at a certain temperature, from warehouses to restaurants. It is important to understand the fundamentals of industrial refrigeration maintenance to ensure these systems function properly and efficiently.
Onda industrial refrigeration is a leader in the field of industrial refrigeration maintenance. With advanced technology and innovative products, they provide solutions to ensure that all parts of an industrial refrigeration system run optimally. By providing expert advice and high-quality products, they ensure that businesses can keep their systems functioning properly, allowing for the best possible performance.
Page Contents
Importance Of Regular Inspections And Maintenance
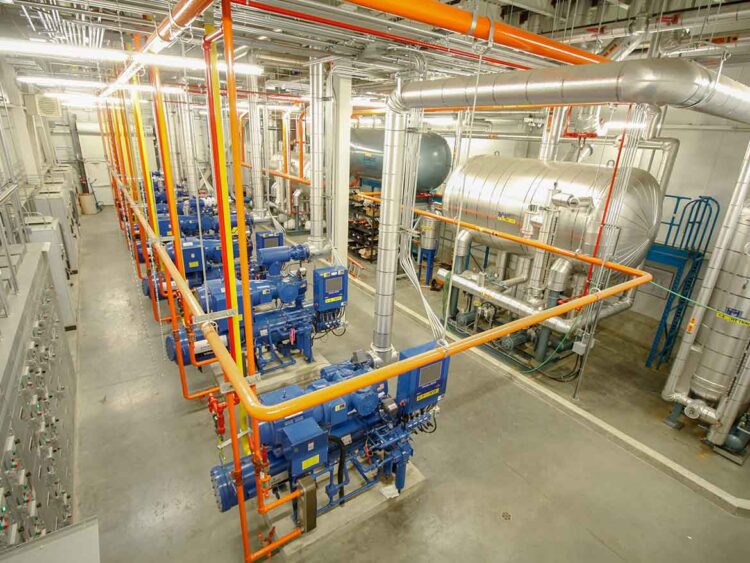
Source: esmagazine.com
Industrial refrigeration systems are critical components of various manufacturing and food processing operations. Regular inspections and maintenance are essential to ensure they remain in optimal working condition. Without timely inspections and maintenance, the efficiency of these systems can deteriorate, leading to increased energy costs, higher repair bills, lost production time, and a shorter lifespan of the system.
Regular inspections and maintenance of industrial refrigeration systems allow technicians to detect potential problems early on, preventing them from becoming larger issues. These inspections can identify worn or damaged parts that need to be replaced and provide an opportunity to check for leaks and other signs of improper operation. Additionally, regular maintenance can help extend the system’s life, reduce energy costs, and maintain a safe working environment.
Components And Their Functions
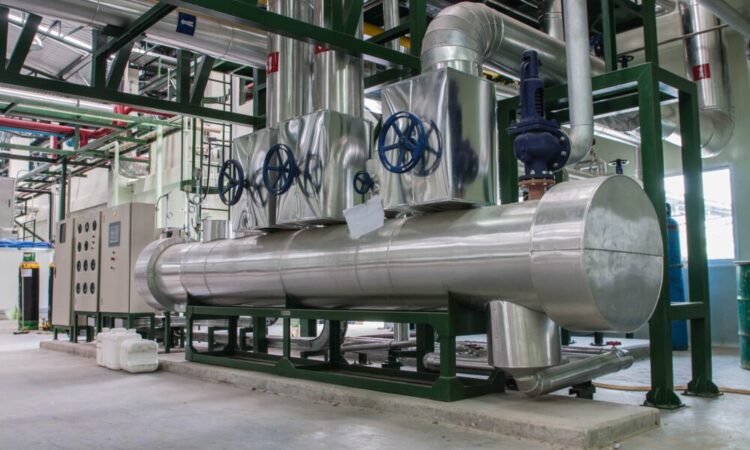
Source: techbullion.com
An industrial refrigeration system typically consists of four main components: a compressor, condenser, evaporator, and expansion device. The compressor draws the refrigerant (usually a Freon-type gas) from the evaporator and compresses it into a high-pressure gas. This gas is then passed through the condenser, which is cooled and condensed into a liquid.
The liquid is then moved through the expansion device, where pressure is released, allowing it to evaporate, creating cold air. This cold air is passed through the evaporator coil and circulated throughout the space or product being cooled. The compressor then picks it up, and the cycle starts again. Proper maintenance of each component is essential in ensuring a refrigeration system runs efficiently and effectively.
Maintaining the compressor, condenser, evaporator, and expansion device components of an industrial refrigeration system and understanding vibration analysis can help ensure the system’s performance, longevity, and energy efficiency. To keep the compressor in good working order, it is essential to regularly check the oil levels and clean any accumulated debris from the filter.
The condenser should be checked regularly for signs of corrosion or other damage and free of dust, dirt, leaves, etc. Both the evaporator and expansion device should be inspected regularly for clogs, leaks, or other damage. Checking the system for any loose connections and ensuring all electrical components are properly connected is also important in keeping a refrigeration system running smoothly. Properly maintaining an industrial refrigeration system’s four main components can help ensure that it runs safely and effectively for years to come.
Common Problems That Can Arise
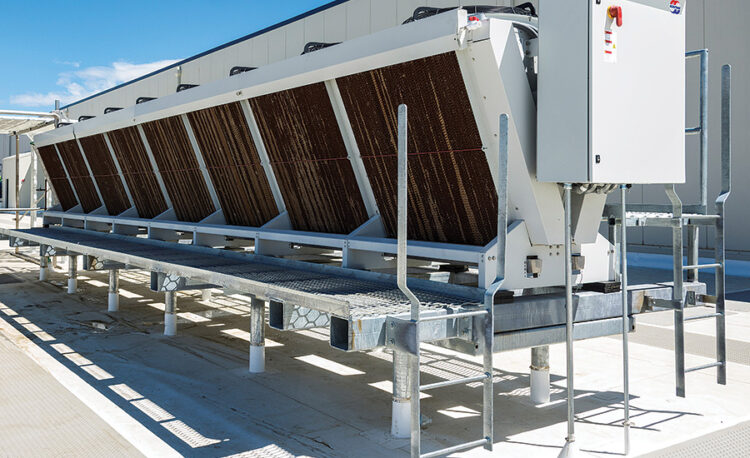
Source: process-cooling.com
While designed to provide precise temperature control, industrial refrigeration systems require careful maintenance and monitoring to ensure they continue to work effectively. Common problems with industrial refrigeration systems include leaks, improper cooling, and electrical issues.
Leaks in a refrigeration system can cause pressure loss and weaken the entire system. If not addressed, the leakage can cause wear and tear on other components or even contaminate the coolant. To find and repair leaks, technicians must inspect all visible components for damage and use dedicated leak-detection equipment.
Improper cooling is also a common problem with industrial refrigeration systems. This can occur when a system is not calibrated correctly when components are worn or damaged, or due to air bubbles. To identify and correct this issue, technicians must check all mechanical and electrical components and take readings from thermometers and pressure gauges installed in the system.
Lastly, electrical issues can arise with refrigeration systems that are not properly maintained. Defective wiring, faulty sensors, or worn-out parts can cause these. To identify and resolve these issues, technicians must use electrical testing equipment to detect any current or voltage irregularities in the system. This is a vital step in ensuring the system continues operating safely and efficiently.
Best Practices For Troubleshooting And Fixing Common Problems
Industrial refrigeration systems are complex and require regular maintenance to maintain optimal functioning. Troubleshooting and fixing common problems in an industrial refrigerator can be daunting, but following some best practices can help ensure that the job is done correctly and efficiently.
The first step in troubleshooting any problem with an industrial refrigerator is accurately diagnosing the issue. This can be done by carefully examining all of the components and how they are connected and running tests on the system itself. Once the issue has been identified, it’s important to take action quickly and correctly so that further damage doesn’t occur.
Proper safety precautions should always be taken when performing maintenance or repairs on an industrial refrigerator. This includes wearing protective clothing and eyewear and disconnecting the electrical power before beginning any work. It’s also important to ensure that all parts are properly aligned and securely connected and double-check every connection before turning on the system again.
Periodic maintenance is also key to ensuring an industrial refrigerator’s long-term health and performance. This should include regular cleaning and lubricating of all moving parts, checking for signs of wear or damage, replacing faulty components, and inspecting the system for potential leaks or other issues.
Conclusion
We’ve discussed the fundamentals of industrial refrigeration maintenance, from understanding how to maintain and inspect your system to preventing costly breakdowns properly. By following these tips, you can ensure that your system runs efficiently and safely for years. Regularly checking up on your equipment is essential to keep it running optimally.
Additionally, ensuring that all personnel involved in the operation are adequately trained will help reduce downtime due to improper use or mishandling of components. With proper care and attention, you should be able to enjoy a reliable refrigeration system for many years into the future!